Biodegradable Polystyrene Alternative using Wood: Packaging Solutions by Swedish Startup
SUSTAINABILITYPACKAGING
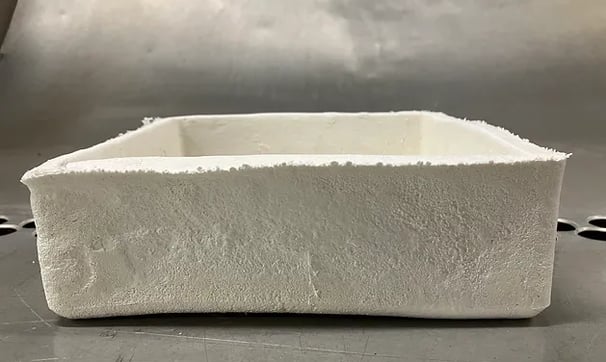
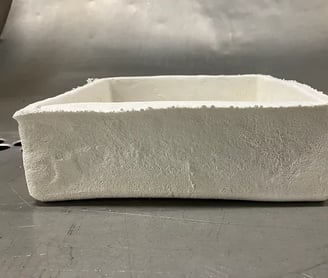
The global reliance on expanded polystyrene (EPS) and expanded polypropylene (EPP) in packaging and construction has long posed environmental challenges. These materials, derived from fossil resources, contribute significantly to landfill waste and are notoriously difficult to recycle. Cellofibers Sweden AB addresses this pressing issue with a new invention: a lignocellulose-based method to produce lightweight granules for flexible, molded foamed packaging. Their innovative material, known as Cellofiber Granule/Cellofiber Foam (CFG/CFF), is biodegradable and recyclable, aiming to replace EPS in various applications, including packaging, construction, and transportation. This innovation not only minimizes fossil resource dependency but also integrates seamlessly into existing production systems while being recyclable with paperboard waste streams.
The Problem with Conventional Packaging Materials
Expanded polystyrene and polypropylene are widely used for their lightweight and shock-absorbing properties. However, their production consumes millions of tons of fossil resources annually, and their recycling rates are dismally low. Some landfills are estimated to comprise 25–35% EPS waste by weight. The need for an environmentally friendly, functional alternative is more critical than ever.
A Lignocellulose-Based Solution
Cellofibers Sweden AB’s patent pending method centers on utilizing lignocellulosic materials, which are abundantly available from sustainable sources such as pulp, recycled paper, or agricultural residues like bagasse and straw. The process involves creating lightweight granules with a composition of more than 95% lignocellulose. These granules can be molded into various forms, including shock-absorbing packaging, disposable cups, trays, and insulating materials. Founded on technology stemming from research at MoRe Research Örnsköldsvik AB, part of RISE, CellOfibers is headquartered in Lindesberg, Sweden. The company emphasizes that its solution is a "drop-in" replacement, allowing manufacturers to transition from EPS to their fiber-based material without the need for new equipment or machinery investments.
The manufacturing process involves:
Preparation of Lignocellulose Suspension: A pumpable aqueous suspension of lignocellulosic material is created.
Optional Additives: Plasticizers and debonding agents may be added to enhance flexibility.
Mixing with Expandable Particles: Thermally expandable particles, such as microspheres, are mixed into the suspension.
Binding Agents: Polymeric flocculants or binding agents ensure homogeneity.
Dewatering: The mixture is dewatered using centrifugation or press filters to achieve a solid content of 20–40%.
Granulation and Drying: The material is granulated using high-shear granulators or fluid beds and then dried to achieve 70–100% dryness, using methods like hot air or infrared radiation.
Applications and Benefits
The granules produced through this method are versatile and can be molded into flexible and foamed products with densities ranging from 0.05 to 0.8 g/cm³. These products are suitable for:
Disposable drinking cups and food containers
Shock-absorbing packaging for electronics
Insulation materials for buildings
Recyclable food trays and plates
Additionally, these granules can serve as a drop-in replacement for EPS in existing production systems, significantly reducing the environmental footprint.
Innovation in Foamed Product Manufacturing
The process also includes a method to expand the granules into foamed products using steam, which achieves densities as low as 0.025 g/cm³. This method minimizes the use of fossil-based polymers to less than 5%, aligning with sustainability goals while delivering excellent performance.
Environmental and Economic Impact
This innovation addresses several key environmental concerns:
Sustainability: By relying on lignocellulosic materials, the process drastically reduces the dependence on fossil resources.
Recyclability: The products can be recycled alongside paper and cardboard waste, promoting circularity.
Reduced Waste: The method eliminates issues like dusting and material loss during production.
Economically, the technology provides a cost-effective solution for manufacturers seeking sustainable alternatives to EPS and EPP.
By leveraging lignocellulose materials and innovative manufacturing processes, the company offers a practical, environmentally friendly alternative to traditional fossil-based packaging. This invention not only reduces the ecological footprint of packaging materials but can also sets a new standard for sustainable product design in the global marketplace.