GEA's Zero Gasket Homogenizer: Know the Innovation behind GEA's New Homogenizers
BEVERAGESSUSTAINABILITYDAIRY & ALTERNATIVES CONFECTIONARY
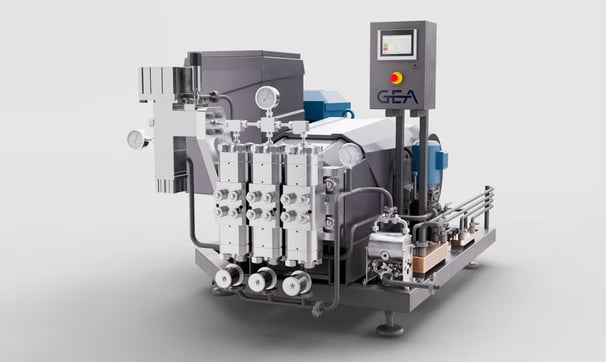
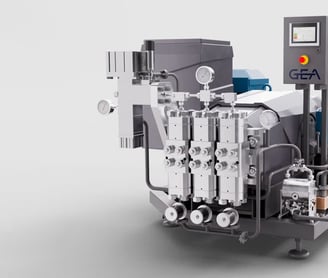
Homogenization, an essential step in numerous industries, faces significant challenges in handling high-pressure, aggressive environments. Addressing these issues, GEA's latest patent application introduces a new compression head design, promising enhanced efficiency, durability, and reduced maintenance needs.
The Challenges of High-Pressure Homogenization
Homogenization, especially at pressures exceeding 600 bar, is a critical step in industries such as:
Food and Beverage: Stabilizing emulsions, enhancing shelf life, and refining particle size—particularly in dairy applications.
Pharmaceuticals: Extracting intracellular materials by breaking cell membranes.
Chemical Manufacturing: Modifying particle structures and producing nanostructures like graphene and carbon nanotubes.
However, traditional systems face recurring challenges:
Frequent Gasket Failures: Conventional gaskets made of plastic or elastomeric materials wear out quickly under high pressure, temperature fluctuations, and exposure to aggressive chemicals.
High Maintenance Downtime: Replacing worn-out components, especially O-rings and anti-extrusion rings, leads to significant downtime and increased operational costs.
Durability Limitations: Components fail due to cavitation, fibrous fluids, or extreme pressure fluctuations, further compounding operational inefficiencies.
GEA’s Solution
The patent offers a compression head design that eliminates the limitations of traditional systems by introducing a metal or ceramic valve seat that also functions as a gasket. This innovative dual-purpose component is a key differentiator, bringing significant advantages:
1. Integrated Valve Seat-Gasket Design
The valve seat, made of durable materials, serves as both the sealing and structural component.
This reduces the number of components, eliminating the need for traditional O-rings or anti-extrusion rings.
2. Superior Material Selection
Constructed from materials like AISI 316L, Silicon Nitride, Tungsten Carbide, or Zirconia, the valve seat withstands:
High and pulsing pressures.
Extreme temperatures (both high and sub-zero).
Cavitation and exposure to abrasive or aggressive fluids.
The choice of materials extends the lifetime of the component far beyond that of traditional gaskets.
3. Simplified Assembly and Maintenance
The valve seat features a cylindrical design with rotational symmetry, allowing for faster and easier installation or replacement.
The need for additional sealing elements (like O-rings) is eliminated, reducing maintenance downtime and overall complexity.
4. Enhanced Performance Under Extreme Conditions
The new design performs exceptionally well under high-pressure applications, even those exceeding 2,000 bar.
It resists deformation, wear, and rupture caused by challenging conditions, ensuring consistent performance over extended periods.
Advantages for Industries
GEA’s patent pending compression head design offers several tangible benefits:
Reduced Downtime: With fewer components to replace and a simplified assembly, maintenance schedules are minimized, boosting productivity.
Cost Efficiency: The longer lifespan of the valve seat translates into fewer replacements, cutting operational costs significantly.
Versatility Across Sectors: From stabilizing dairy emulsions to facilitating nanotechnology applications, the compression head adapts seamlessly to a variety of processes.
By addressing long-standing issues in high-pressure homogenization, this innovation paves the way for more reliable, efficient, and durable processing equipment. Industries requiring precise homogenization under challenging conditions now have access to a solution that reduces wear and tear, optimizes uptime, and enhances overall process quality.
GEA's product in market - GEA Rhino
The company has used this technology in their Rhino range of homogenizers that are designed specifically for those challenging industrial products: abrasive, adhesive, or high-solvent content, used in the production of batteries, carbon nanotubes, and nanocellulose that require high pressures, up to 2000 bar. It can withstand abrasion, pressure and temperature fluctuations, and cavitation phenomena that can occur inside the compression head.