University of Georgia’s Innovation in Home Compostable Adhesives
PACKAGING
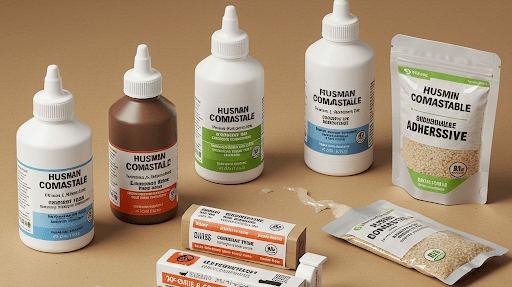
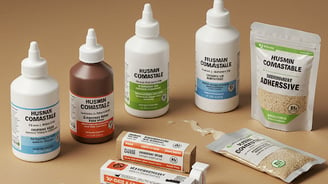
This is an AI generated illustration and does not represent actual product or service.
In an era where sustainability and environmental responsibility are paramount, the development of biodegradable and compostable materials has become a critical focus for researchers and industries alike. Adhesives, particularly pressure-sensitive adhesives (PSAs), are ubiquitous in everyday products, from labels on food packaging to tapes and stickers. However, traditional adhesives are often made from non-biodegradable materials, contributing to environmental pollution and waste. Addressing this challenge, the University of Georgia has developed a groundbreaking home compostable adhesive composed of a biodegradable polyester. This innovation offers a sustainable alternative to conventional adhesives, combining environmental benefits with the mechanical and physical properties required for commercial applications.
The Problem: Non-Biodegradable Adhesives
Adhesives, especially pressure-sensitive adhesives, are essential in various industries, including packaging, labeling, and consumer goods. However, most adhesives are derived from petroleum-based materials, such as acrylics and synthetic rubbers, which are non-biodegradable and persist in the environment for decades. When disposed of, these adhesives contribute to plastic pollution, microplastic contamination, and landfill waste.
The growing demand for sustainable products has highlighted the need for adhesives that can break down naturally without harming the environment. While some biodegradable adhesives exist, they often lack the performance characteristics required for commercial use, such as tack, peel strength, and durability. The University of Georgia’s invention addresses this gap by creating a home compostable adhesive that not only meets environmental standards but also delivers the mechanical properties needed for practical applications.
The Solution: A Biodegradable Polyester-Based Adhesive
The University of Georgia’s patent describes a home compostable adhesive composed of a unique polyester. This polyester is synthesized from renewable resources and designed to break down completely in home composting conditions, leaving no harmful residues. The adhesive is particularly suitable for use as a pressure-sensitive adhesive (PSA), making it ideal for applications such as labels, tapes, and stickers.
Key Components of the Polyester
The polyester is composed of the following key components:
1. Diol Residues: The polyester includes residues of diols such as 1,3-propanediol, 1,4-butanediol, or a combination of both. These diols provide the backbone of the polymer, influencing its flexibility and thermal properties.
2. Dicarboxylic Acid Residues: The polyester incorporates residues of two dicarboxylic acids: succinic acid and glutaric acid. These acids contribute to the polymer’s structure and mechanical properties, such as strength and elasticity.
3. Sugar Residues: A unique feature of the polyester is the inclusion of sugar residues, which act as crosslinkers. The sugar component, such as sorbitan monooleate, enhances the adhesive’s cohesive strength and modifies its rheological properties. The sugar content can be adjusted to tailor the adhesive’s performance, such as its tack and peel strength.
Synthesis of the Polyester
The polyester is synthesized through a polycondensation reaction, where the diols, dicarboxylic acids, and sugar are mixed and heated under controlled conditions. The reaction is carried out at temperatures between 100°C and 200°C, with the addition of a catalyst to facilitate the polymerization process. The resulting polyester is amorphous, with a low glass transition temperature (Tg) of less than 25°C, making it suitable for use as a pressure-sensitive adhesive.
Compostability
One of the most significant advantages of this adhesive is its home compostability. The polyester is designed to break down completely under home composting conditions, as defined by standards such as AS 5810 and TÜV AUSTRIA OK Compost Home. Respirometry tests conducted at 21°C demonstrated that the adhesive mineralizes over 90% of its organic carbon within 90 days, far exceeding the requirements for home compostability.
Benefits of the Home Compostable Adhesive
The University of Georgia’s invention offers several advantages over traditional adhesives:
1. Environmental Sustainability: The adhesive is made from renewable resources and is fully compostable, reducing its environmental impact and contributing to a circular economy.
2. Performance: The adhesive exhibits excellent tack, peel strength, and cohesive properties, making it suitable for a wide range of commercial applications. Its viscoelastic properties are comparable to those of conventional PSAs, ensuring reliable performance.
3. Versatility: The adhesive can be used in various applications, including labels for food packaging, tapes, and stickers. It is particularly well-suited for produce labels, where compostability is a significant advantage.
4. Customizability: The adhesive’s properties can be tailored by adjusting the composition of the polyester, such as the ratio of diols, dicarboxylic acids, and sugar. This allows for the development of adhesives with specific performance characteristics for different applications.
5. Regulatory Compliance: The adhesive meets stringent standards for home compostability, ensuring that it can be safely disposed of in home composting systems without leaving harmful residues.
Applications of the Home Compostable Adhesive
The adhesive has widespread commercial applicability, particularly in industries where sustainability is a priority. Some key applications include:
1. Food Packaging Labels: The adhesive is ideal for produce labels and other food packaging applications. Its compostability ensures that labels can be disposed of along with organic waste, reducing contamination and waste.
2. Tapes and Stickers: The adhesive can be used to produce compostable tapes and stickers, offering a sustainable alternative to conventional products.
3. Consumer Goods: The adhesive can be incorporated into various consumer products, such as removable labels and repositionable adhesives, providing both functionality and environmental benefits.
Testing and Validation
The adhesive has undergone rigorous testing to validate its performance and compostability:
1. Rheological Analysis: The adhesive’s viscoelastic properties were evaluated using a parallel plate rheometer. The results confirmed that the adhesive has the appropriate balance of elasticity and viscosity for use as a PSA.
2. Loop Tack Testing: The adhesive’s instant tack was measured using ASTM D6195-03. The results demonstrated that the adhesive has tack properties comparable to those of conventional PSAs.
3. Biodegradation Testing: The adhesive was tested under home composting conditions at 21°C. Respirometry analysis showed that the adhesive mineralized over 90% of its organic carbon within 90 days, meeting the requirements for home compostability.
The University of Georgia’s development of a home compostable adhesive represents a significant advancement in sustainable materials science. By combining environmental benefits with the mechanical properties required for commercial use, this innovation offers a viable alternative to traditional non-biodegradable adhesives. As industries and consumers increasingly prioritize sustainability, this adhesive has the potential to revolutionize the adhesives market, reducing environmental impact and contributing to a more sustainable future.
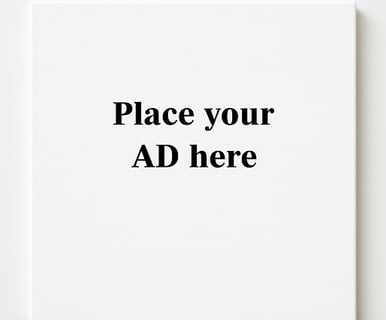
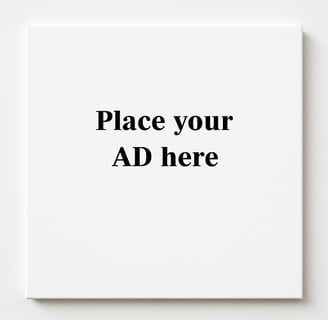